Introduction
Are you looking to start a new profitable business? Is manufacturing products while ‘not harming’ nature and planet Earth what gives you motivation? Well, here is the answer and one of the best options for your business, Sugarcane Bagasse Products Manufacturing Plant.
What kind of products those would be, you ask? There are plenty of options and diverse product ranges to make which have applications in table wares, takeaway packaging, cups, electronic items, industrial components, household goods, cosmetics packaging, medical disposables, hospital disposables, horticulture, and more.
Embrace a sustainable manufacturing process that significantly reduces plastic consumption worldwide, mitigates pollution, and minimizes harm to nature. According to some researches, shockingly, plastic production has surged from 2 million tonnes in 1950 to a staggering 400 million tonnes in 2019, with a substantial portion contributing to environmental degradation. Approximately 200,000 tonnes of plastic find their way into the oceans annually, exacerbating pollution concerns. Opting for sustainable products presents a pivotal solution to combat this crisis.
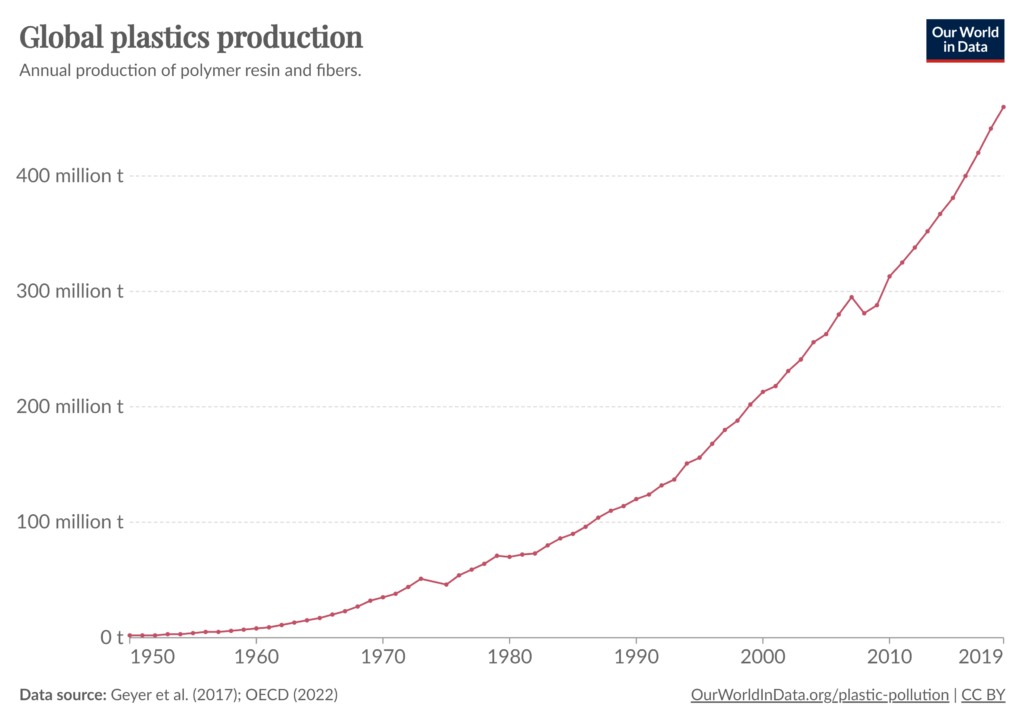
Image Sorce – https://ourworldindata.org/
In this article, I will guide you in detail about how to start a sugarcane bagasse product manufacturing plant, what are the requirements for it, what would be the process to set up such a plant, the documentation to start a new plant of sugarcane bagasse product, and most importantly, the budget and the return on the investment (ROI) of this business.
Our comprehensive guide delves into the intricacies of establishing a sugarcane bagasse product manufacturing plant. Embark on a journey towards eco-friendly entrepreneurship—unleash the potential of Sugarcane Bagasse Products Manufacturing and make a positive impact on the environment while securing profitable returns.
What do you need to start a sugarcane bagasse products plant?
Let’s get to know about the production cycle of the products from Sugarcane Bagasse first. Delve into the intricate production cycle of Sugarcane Bagasse products, a sustainable and eco-friendly alternative. The journey begins with two primary methods: utilizing sugarcane bagasse as the raw material or commencing production using bagasse pulp sheets obtained from reliable suppliers.
The bagasse pulp sheet is a result of processing sugarcane bagasse through a series of refining processes. These sheets serve as the foundational raw material for the subsequent stages of production. The well-defined cycle for crafting sugarcane bagasse products initiates with stock preparation. This stage involves employing pulping machines and other machinery to create a slurry with optimal consistency.
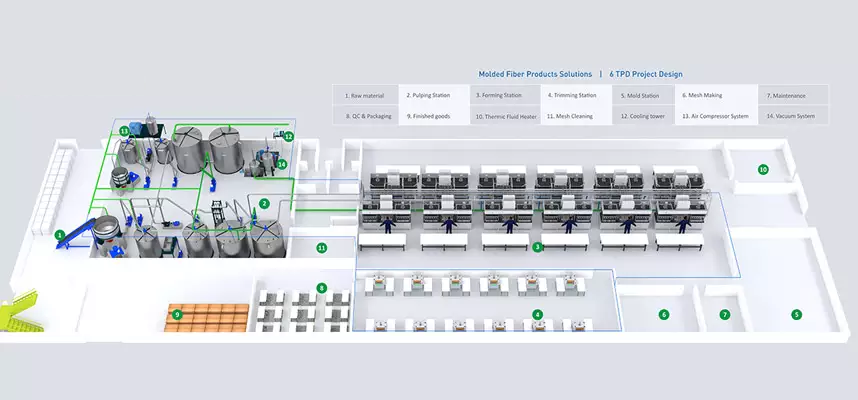
Moving forward, the forming section takes center stage, housing various forming machines. Utilizing specific molds, these machines enable the production of a diverse range of products. Subsequently, the product undergoes a drying process within the inbuilt section of the forming machines before progressing to the trimming section.
At the trimming section, the product receives its final touches and finishing, ensuring a polished and refined appearance. Following this, the product seamlessly advances to the packaging section and, ultimately, the dispatch phase.
Embarking on this production journey requires a set of essential elements, including land, machinery, manpower, and raw materials. However, to ensure a smooth initiation of your molded fiber product plant, meticulous attention to detail is crucial. To assist in this endeavor, a comprehensive checklist has been curated, covering all essential aspects to consider when starting your venture. Explore the checklist to guarantee a seamless and successful establishment of your Sugarcane Bagasse product manufacturing plant.
Check-List:
- Know the process
- Know your market
- Land and location
- Water and Electric Supply
- Plant layout
- Documentation and licensing
- Machinery and molds
- Staff
- Budget, Expenses & Return on Investment (ROI)
Let’s see all these factors step by step and get closer to your dream of being an industrialist of eco-friendly molded fiber products.
Know the process
When starting to build any business one of the main factors is to know the process. You should know the exact procedure to follow to get your dream project succeed.
To start a sugarcane bagasse product manufacturing plant your process follows as mentioned in the checklist above. The next step in the process is to know your market.
Know your market
Before starting any business, comprehensive market research is crucial. Embarking on a new business venture demands a thorough understanding of your market, and the molded fiber products industry is no exception. Conducting comprehensive market research is essential to grasp the dynamics of the market, anticipate future trends, assess competition, identify opportunities, and strategize effectively.
In this particular sector of molded fiber products, the scope of the profit and the business growth is incredible. As per the research of Future Market Insights (FMI), the global bagasse tableware products market value is expected to surge from US$ 2,985.1 million in 2023 to an impressive US$ 5,230.5 million by 2032.
There is a huge rise in the future for this market. Acquiring a deep understanding of your market enables you to formulate effective production and marketing strategies, ensuring a swift return on investment and higher profits in no time.
Beyond market awareness, there are additional factors to consider when establishing a manufacturing plant for sugarcane bagasse products. The design and capacity of your facility should align with your targeted production volume. In the case of molded fiber products, daily production quantities vary widely. Let’s delve into the considerations for a 6-tonne per day production volume.
Land and Location
After market research and knowing the business when you are ready to build the plant, you need land for it. Since we are considering the plant for the production volume of 6TPD we will discuss the requirements accordingly.
For a plant targeting a production volume of 6TPD, the requisite land area is approximately 1 acre, equivalent to around 43.5 thousand square feet. This expanse is strategically apportioned into distinct zones, comprising a shaded area and an open area. The shaded region plays a crucial role as it accommodates raw material storage, production infrastructure, packaging facilities, and the dispatch area. Specifically, the shaded area required for a 6TPD plant encompasses approximately 30,000 square feet.
In addition to determining the physical dimensions of the land, careful consideration must be given to its location. Optimal positioning is essential to ensure an adequate supply of water, reliable power sources, and seamless connectivity for the transportation of both raw materials and finished products. These factors collectively contribute to the overall efficiency and viability of the manufacturing facility.
Water and Power supply
In the operational dynamics of a molded fiber production plant, the availability of water holds utmost significance. It is crucial for setting up sugarcane bagasse product manufacturing plants to have a sufficient water supply without fail.
In parallel, the power supply is a pivotal aspect that demands meticulous attention in the planning stages of your envisioned project. For a production target of this magnitude, it is recommended to install a power supply system with a significant capacity after discussing with your project engineers
Ensuring a robust and adequately dimensioned power supply infrastructure is imperative to sustain the seamless and efficient operation of the manufacturing process, contributing significantly to the success of your project.
Plant layout
Once the land and location for your upcoming project are confirmed, the next critical step is the development of the plant layout. Initiating the construction of the factory requires a meticulous analysis of the site and the establishment of an optimal plant layout. Engaging with companies specializing in new plant setups proves instrumental in achieving this objective. Leveraging their expertise not only facilitates the efficient execution of the layout but also allows you to focus on other aspects of the project while minimizing the risk of errors.
There are numerous firms offering comprehensive manufacturing solutions, out of which a few top manufacturing solution providers necessitate thorough research and analysis of the land to provide a holistic engineering solution. It is imperative to entrust this task to an experienced and expert company well-versed in the intricacies of the process.
This extensive undertaking encompasses various aspects such as plant layout, equipment sizing, tank and pump specifications, line valves, instrumentation, 3D planning, and interconnections. Identifying a reliable partner for your engineering needs is crucial to gaining a comprehensive understanding of this multifaceted process. By collaborating with a seasoned professional, you can ensure a seamless and well-organized plant layout, setting the foundation for the success of your project.
Documentation and Licensing To Start a Molded Fiber Product Manufacturing Plant
While your reliable partners for your engineering solutions and plant layout work on their task you can free yourself to complete the other important documentation processes to start your plant. There are some licenses or certificates you need to take care of before and after starting your production line. Some of the important certificates/licenses to start a molded fiber products manufacturing plant are mentioned below. These certifications may vary and may need additional documentation depending on the jurisdiction you are planning to set up your plant.
- Business Registration: Register your business with the appropriate authorities. This can include registering as a Private Limited Company, Limited Liability Partnership (LLP), or any other suitable business structure.
- Business License: Obtain a general business license to operate legally in the chosen location. This is typically issued by local government authorities.
- Environmental Clearance: It is necessary to get a certificate from the Pollution Control Board to start manufacturing in the plant.
- Factory License: In many jurisdictions, a factory license or industrial permit (Consent to Establish) is required to establish and operate a manufacturing plant.
- Zoning Clearance: Ensure that the chosen location complies with zoning regulations and obtain any necessary zoning clearances.
- Waste Management License: To ensure that you are not distributing your waste in nature, you may need a waste management license to handle and dispose of waste properly.
- Fire Safety Certificate: Ensure that the facility meets fire safety standards, and obtain a fire safety certificate if required.
- Quality Certifications: Depending on the products you manufacture, obtaining quality certifications such as ISO certification may be beneficial for both regulatory compliance and market acceptance. This may be needed after the actual production and not to be needed to construct the plant.
- Trademark Registration: Consider registering trademarks for your molded fiber products to protect your brand.
- Employer Identification Number (EIN): If applicable, obtain an EIN from tax authorities for tax purposes.
- Employee Provident Fund (EPF) and Employee State Insurance (ESI) Registration: If you have employees, register for EPF and ESI to comply with labor welfare regulations.
- Factory License: Obtain a factory license under the Factories Act, 1948. This license is issued by the State Directorate of Industrial Safety and Health. (India)
- Goods and Services Tax (GST) Registration: Register for GST, a unified tax applicable to the manufacture and sale of goods and services in India.
- Import-Export Code (IEC): If you plan to import or export materials or finished products, obtain an Import-Export Code from the Directorate General of Foreign Trade (DGFT).
- Bureau of Indian Standards (BIS) Certification: Depending on the products, you may need BIS certification to ensure that your products meet specified quality standards.
The above-mentioned certifications may vary and may add some if needed according to the location and jurisdiction you are planning to set up your plant. But to get an idea about the documentation you can refer to the above certifications.
Consulting with an expert for your plant will get your documentation done smoothly.
Machinery and Molds Required For Molded Fiber Product Manufacturing Plant
In the realm of molded fiber product manufacturing, the nucleus of a successful production line lies in the meticulous selection of machinery and molds. These critical components demand careful consideration, as aligning your machinery with production targets and strategic goals is paramount for budgetary efficiency.
For molded fiber products, considering that you are starting your production line with bagasse pulp sheets as raw material, it becomes imperative to identify the specific machinery essential for the process. Key equipment required includes:
- Stock Preparation (pulping tanks, refiners, etc)
- Forming Machines (semi-automatic manual, semi-automatic robotic, fully automatic)
- Molds
- Trimming Machines
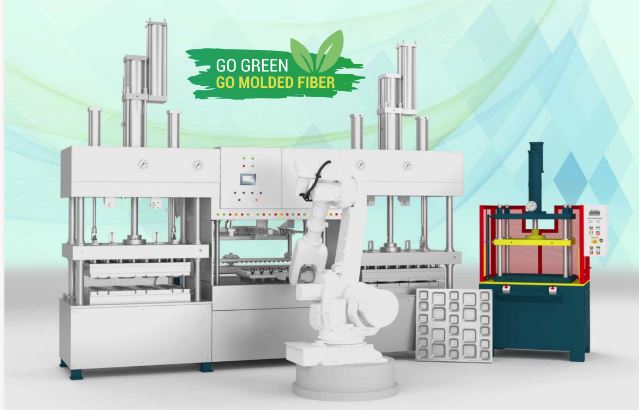
These foundational machines serve as prerequisites for any molded fiber product manufacturing plant. Additionally, optional equipment such as conveyors, packaging machines, and a TFH plant for heat treatment can be integrated based on individual plant requirements.
For a production plant with a target output of 6 Tons Per Day (6TPD) utilizing semi-automatic manual machines, the following machinery specifications are recommended:
Machinery | Capacity | Quantity |
Pulping Machines | 6 TPD | Differs |
Forming Machines | 500 kg per day | 12 set |
Trimming Machine | 500 kg per day | 12 set |
Molds | Depend on the size of the product | 12 set |
Staff Requirement For Molded Fiber Product Manufacturing Plant
A fully operational manufacturing facility hinges on the presence and expertise of its operators and staff. The strategic recruitment of skilled professionals is a pivotal undertaking in ensuring the seamless execution of tasks. It is imperative to meticulously assess your operational requirements and staff the facility accordingly.
At times, it becomes indispensable to conduct a thorough analysis to determine whether an operator or a robotic arm is the optimal solution for specific tasks. Evaluating the one-time investment associated with acquiring a robotic arm against the recurring monthly or yearly salary of an operator provides a comprehensive basis for decision-making, taking into account efficiency considerations.
For manufacturing plants equipped with semi-automatic manual molded fiber machines, the following staffing requirements are deemed essential. Engaging experts in the relevant fields ensure a proficient workforce capable of maximizing operational output and efficiency.
Staff requirement for a 6TPD molded fiber manufacturing plant with semi-automatic manual forming machines on 2 shift basis:
Sr. No. | Employee | Expertise | Nos |
1 | Pulp Technician | To operate and review pulp production | 2 |
2 | Pulp Loader | To manage the plant operations and make sure smooth production. | 2 |
3 | Forming Operators | To operate the forming machines | 48 |
4 | Trimming Operator | To operate trimming machine /product finishing. | 24 |
5 | QC and Packaging | To test the quality of the product and packaging | 30 |
6 | Utility and Maintenance | To check the necessary requirements and maintenance | 1 |
7 | Plant Manager | To ensure the swift running of the TFH plant | 1 |
8 | Supervisor | To supervise the plant operations and make sure the smooth production. | 2 |
9 | TFH fuel loader | To manage all the accounting, designing, and official works. | 2 |
10 | Helper | Necessary for any small task, cleaning and other things | 2 |
11 | Marketing Staff | To promote the product and get more clients | 2 |
12 | Office Staff | To manage all the accounting, designing and official works. | 4 |
Budget, Expenses, and Return on Investment (ROI)
Till this point, you have a brief idea about everything that you need to start a sugarcane bagasse product manufacturing plant. The most important thing to start all this is budget. It is crucial to make use of your money at a place where you can make a good return from it. Let’s take a look at what is the budget required to start a molded fiber product plant using sugarcane bagasse as raw material.
The budget of the plant particularly differs on the basis of several things, like the production capacity of the plant, area required, location, availability of power, and other necessary factors. However, the return on the investment from this molded fiber plant is very high and observed to get in 2 to 3 years.
For a 6 TPD capacity Sugarcane Bagasse products manufacturing plant the approx budget is around Rs.9.5 cr. to Rs.10cr (approx. USD 1.1 million to USD 1.2 million).
The production cost of the product sums up to approx. Rs. 130 to Rs. 140 per kg and it can sell up to around Rs. 190 to Rs. 200 per kg in the market.
The measure expenses that are included in the production cost are the salary of the employees, raw material to stock preparation cost, production line cost, water and power supply cost, maintenance, and packaging.
Advantages of sugarcane bagasse product production.
The molded fiber products have an increasing demand in the market. People are becoming aware of the bad impact of plastic products on nature as well as on health. The market size of sustainable products has a vast future scope. Why you should start a molded fiber product manufacturing plant?
Sustainability: An eco-friendly alternative to traditional materials and contributing to sustainable practices.
Reduced Plastic Consumption: A molded fiber product manufacturing plant provides an effective solution by producing items that can replace traditional plastic tableware and packaging.
Market Growth: The market for molded fiber products, particularly in tableware, is experiencing significant growth, presenting a lucrative opportunity for entrepreneurs to capitalize on the increasing demand for sustainable alternatives.
Diverse Product Range: The versatility of molded fiber allows to produce a wide range of products, including table wares, takeaway packaging, cups, electronic items, industrial components, household goods, cosmetics packaging, medical disposables, and more, catering to diverse industries.
Environmental Impact: By choosing molded fiber over plastic, the manufacturing plant contributes to environmental conservation by mitigating pollution, reducing carbon footprint, and promoting the use of biodegradable materials.
Regulatory Support: Governments and consumers alike are increasingly supporting initiatives that promote sustainable practices. A molded fiber product manufacturing plant aligns with these trends, potentially qualifying for incentives, subsidies, or favorable regulatory considerations.
Consumer Preference: With growing awareness of environmental issues, consumers are actively seeking eco-friendly alternatives. Starting a molded fiber product manufacturing plant allows businesses to meet this demand and build a positive brand image.
Innovative Technology: The manufacturing process involves innovative technologies for converting bagasse into molded fiber products, showcasing a commitment to cutting-edge, sustainable production methods.
Reduced Production Costs: Compared to some other eco-friendly alternatives, molded fiber products can be cost-competitive, especially when considering the potential for economies of scale and streamlined production processes.
Positive Return on Investment: With a well-thought-out business plan and adherence to sustainable practices, a molded fiber product manufacturing plant has the potential for a positive return on investment, offering both financial success and environmental benefits.
Conclusion
In conclusion, starting a successful sugarcane bagasse product manufacturing plant presents a promising venture for eco-conscious entrepreneurs seeking both profitability and environmental impact.
This comprehensive guide has illuminated the intricate process of establishing such a plant, from understanding the production cycle and market dynamics to addressing crucial factors like land, water, and power supply, plant layout, documentation, machinery, staff requirements, and budget considerations.
Embracing the production of molded fiber products from sugarcane bagasse not only promotes sustainability but also aligns with the global imperative to reduce plastic consumption. Market research reveals a substantial growth trajectory in the bagasse tableware products market, underscoring the potential for profitable returns. By adhering to meticulous planning, regulatory compliance, and strategic decision-making, aspiring industrialists can embark on an eco-friendly journey, contributing to a greener future while securing a sound return on investment. The outlined checklist serves as a valuable tool, guiding entrepreneurs step by step toward the realization of their dream of becoming successful industrialists in the realm of eco-friendly molded fiber products.