Have you ever wondered how much of tissue a person uses annually? It is approximately 30 rolls per person per year.
The tissue is an item that holds crucial importance in human life and yet is taken as granted by us humans.
Do you know how these thin, smooth and soft tissues are made? Let us make ourselves aware of the tissue making process.
Where is tissue paper made?
Tissue papers are produced in Tissue Mills. The tissue mills are a huge source of providing tissue papers across the world.
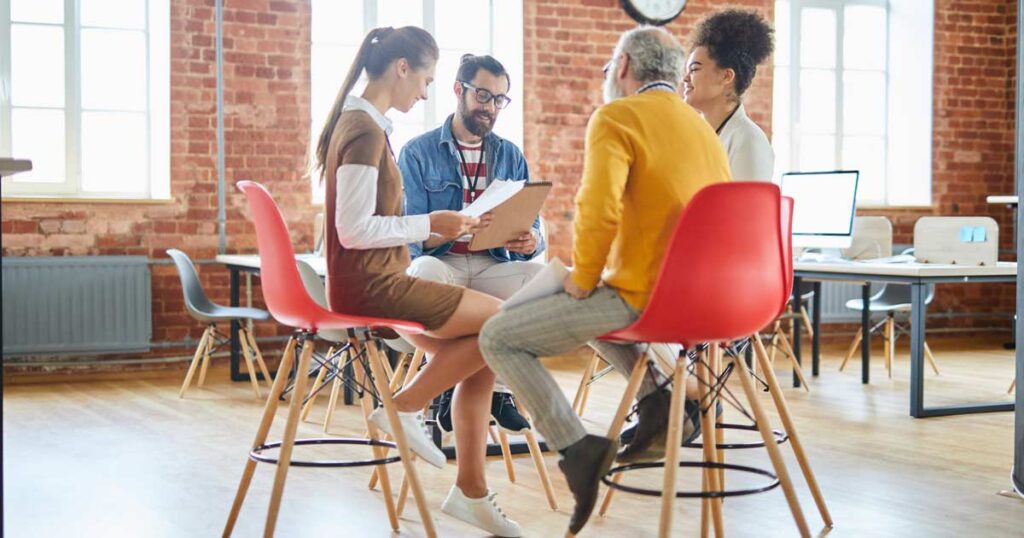
How is tissue made?
The tissue mill works in four main compartments – These are:
1. Stock Preparation
2. Tissue Machine
3. Rewinder
4. Converting Line
Let us discuss the process in brief.
1. Stock Preparation
Stock Preparation is the process where the incoming raw material is made suitable for transforming it into required tissue paper material.
This raw material is mostly fibers.
The fibers are passed through the Pulper Feed System.
The bales of fibers are transported in the pulper through this pulper feed system.
Pulper consists of Pulp Dissolver where the pulp is dissolved.
The dissolved pulp is then transferred to Storage Tower followed by cleaner for cleaning of the pulp.
Further, it is sent to the Refiners, where the material is refined in various stages depending on the desired characteristics of our final product.
The material passes through Blend Chest and Machine Chest before entering the screening phase.
Now, this material, or to be precise, fibers, are sent to the Tissue Machine where the actual process of tissue making begins.
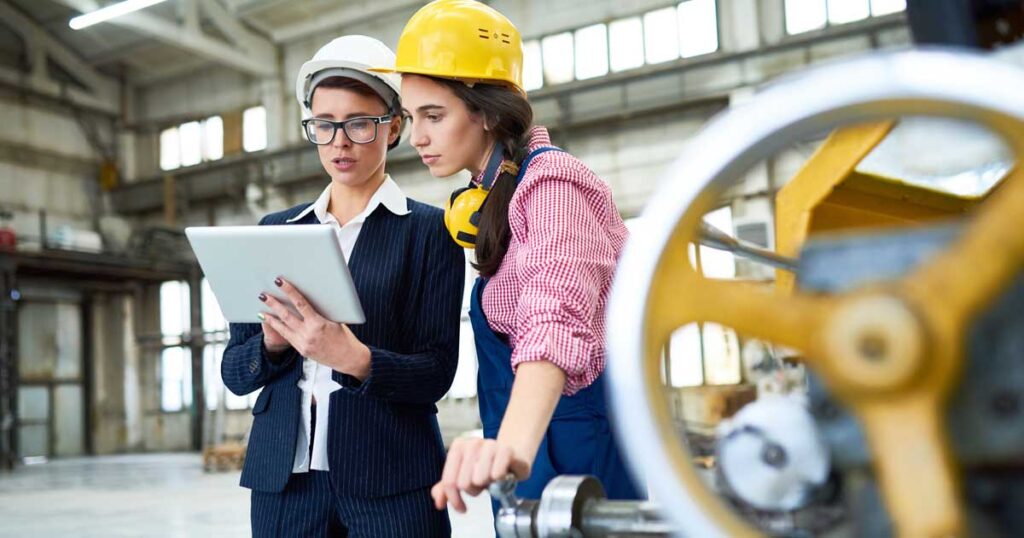
2. The Tissue Machine
The Tissue Machine consists of 6 different parts which carry different processes. Let us name them first:
1. Headbox
2. Press Section
3. Hood
4. Yankee
5. Yankee Doctor
6. Reel
Let us explore each part and what it does in brief
1. Headbox
The fibers received through the stock preparation process, let’s call it stock.
This stock is sprayed into the machine and distributed evenly along the width of the machine in the gap between two rolls.
This stock passes through the headbox to the Press Section.
2. Press Section
The Press Section is divided into 2 parts:
- Suction Roll
- ViscoNip
The stock passes through the Suction Roll to the ViscoNip. Suction Roll is perforated and drains the felt before the press nip.
In ViscoNip, the paper web is pressed using the nip, which contains a long element that presses the felt and belt against the Yankee cylinder.
The paper web is removed in the press nip by squeezing water into the felt.
The stock is further sent to the Drying Cylinder i.e. Yankee
3. Yankee
Here, the cylinder is heated up with steam under pressure and the paper web attaches to the hot surface of the drying cylinder, letting the water evaporate through the paper web.
4. Hood
Hood is a dryer in which heated air is blown onto the paper web to increase drying. The air in the dryer is normally heated with gas burners.
5. Yankee Doctor
Here, the Creping process takes place. The dried stock i.e. the creped structure of the tissue paper is achieved when the paper web is scraped away from the drying cylinder using a steel blade.
6. Reel
The stock which is now closely become a tissue paper is rolled into large cylindrical rollers.
This is the process of a Tissue Machine.
Then comes in play the Rewinder Part.
You would be surprised to know that this entire process that takes place in the tissue machine is completed in merely 1.5 seconds at the speed of 120 Kmph!
3. Rewinder
Rewinding is a 3 step process
1. Piles are joined using unwind stands.
2. Calendering is used for enhanced smoothness property
3. Rolls are slitted into the required width and diameters. The tissue roll is now ready to convert into usable size and structure.
It is then passed to the Converting step.
4. Converting
In the Converting process, the larger sized roll is cut down into smaller regular sized tissue rolls as a final product.
Rolls are unwinded using the embosser or laminator where the sheets are imprinted in the required pattern and ply them back together.
The sheets are winded on a cardboard core. The final product received out from the rewinder is called a log.
There’s a log saw which cuts the log from the rewinder into required widths.
Finally, the product is packed and shipped to the stored for public sale.
In this way, we get our tissue papers which we use daily. If you like the article, let us know in the comments.
We are always excited to hear from our viewers. Have a nice day.